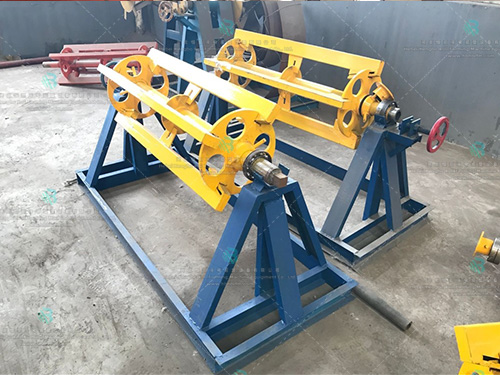
Loading bracket is a device used for auxiliary material loading in industrial production, which can stably support and guide materials into processing machinery. The design of the feeding bracket usually takes into account the characteristics of the material, the requirements of the processing machinery, and production efficiency. The structure and function of the feeding bracket may vary depending on different application scenarios and material types.
Basic structure and working principle
The ordinary feeding bracket is generally composed of a bracket body, a support device, a guiding device, and a control system. The main body of the bracket provides a stable support platform, the support device is used to fix and adjust the position of the material, the guiding device confirms that the material smoothly enters the processing machinery, and the control system is responsible for operating the action of the feeding bracket to adapt to the needs of the production process.
Application scenarios and advantages
Loading brackets are widely used in industries such as mechanical processing, automated production lines, and packaging. They can improve the accuracy and efficiency of material feeding, reduce manual intervention, lower labor intensity, and enhance the overall automation level of production.
Common types and characteristics
Loading brackets can be divided into various types, such as lightweight material racks, heavy-duty material racks, double headed material racks, etc. These types are designed according to the weight, width, and application environment of the load-bearing materials. Lightweight material racks are suitable for processing lightweight and narrow coils, while heavy-duty material racks are suitable for processing heavy-duty and wide coils. The double headed material rack, due to its symmetrical design on both sides, can achieve suitable material changing speed and improve production efficiency.
Maintenance and optimization suggestions
Regular maintenance is very important to confirm the normal operation and extend the service life of the feeding bracket. This includes checking the wear of moving parts, cleaning and lubricating all moving parts, and promptly replacing damaged parts. In addition, according to changes in production demand, the feeding bracket can be optimized and modified to improve its performance and adaptability.
In summary, ordinary feeding brackets are key equipment for improving production automation and efficiency, with diverse designs and suitable for various industrial production scenarios. By reasonable maintenance and timely optimization, its performance and advantages can be further improved.