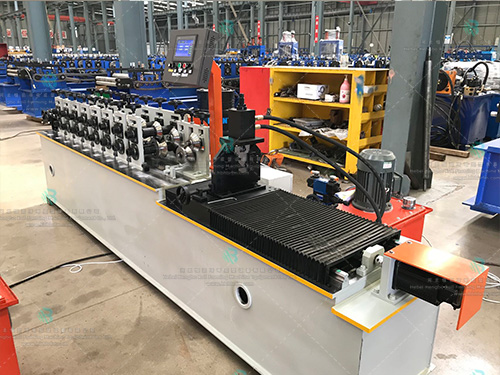
Keel machine is a mechanical equipment that uses strip steel as raw material and continuously cold-rolled to produce complex cross-sectional profiles, such as light steel keels, painted keels, card keels, and other building profiles. This type of equipment typically uses a PLC control system to confirm the automation and accuracy of the production process. The characteristics of the keel machine include high rolling capacity, moderate production speed, reasonable total installed capacity, and small production footprint. The bed of the equipment is usually made of welded steel plates and undergoes tempering treatment to eliminate internal stress and extend its service life. The forming frame is mostly made of cast iron structure, and the roller shaft and forming mold are made of high-quality materials to protect the strength and practicality of the equipment.
The working principle of the keel machine mainly involves placing steel on the machine, contacting the rollers driven by the reducer, feeding and locking through the compressed handle, starting the motor oil pump group, and adjusting the required pressure through the overflow valve with the high-pressure oil output from the electric oil pump. It enters the aggregation block and flows to the electro-hydraulic valve. The hydraulic valve and jog switch control the oil cylinder to work. When the I-beam is compressed with three supporting rollers without bending deformation, the calculation begins. The length of the oil cylinder pushing forward is 10mm-15mm each time. The main motor rotates forward and backward to work with the I-beam, and the operation is repeated to achieve the desired effect. This design enables the keel machine to have the characteristics of smooth transmission and high pressure during operation, which can effectively protect the equipment from long-term and high-intensity operation, and has a long service life.
The application range of the keel machine is wide. It can not only process various cross-sectional profiles, such as light steel keels, painted keels, as well as complex cross-sectional profiles such as high-speed guardrails and steel lined door frame profiles, but also produce various cold bending and painting machine equipment. The production control of these devices is completed through finger touch, such as speed adjustment, pressure adjustment, coding text setting, production file viewing, etc., all of which are controlled through the configured 17 inch control screen. Intelligent control generates protection for a daily production capacity of 120-160 square meters/8 hours, with excellent processing accuracy and protection within 0.3, thus protecting the keel connection more tightly and ensuring the stability of the structure.
In addition, the design and manufacturing of the keel machine focus on safety, adopting multiple safety protection measures to confirm safety during normal production processes. The body and forming frame have undergone special treatment, such as tempering of steel plate welded parts to eliminate internal stress and avoid deformation of the body; The formed frame is made of cast iron structure and has undergone tempering treatment to protect its high strength and long service life. The roller shaft and forming mold are made of 40Cr and GCr15 materials, respectively, and undergo quenching and tempering treatment to achieve the required hardness and practicality. The transmission structure of the entire equipment is a gearbox transmission, and it is confirmed that the equipment can still maintain its effectiveness and stability under long-term high-intensity operation.